Tube Forming
As GoodFabs works mainly with exotic metals, such as inconel and titanium, most of the sizes of the tubes we use to make exhaust manifolds are not readily available.
All our inconel tube is made in-house from a flat sheet, giving us full control over all the aspects of production from the outer diameter to wall thickness, enabling us to create the most complex exhaust systems while optimising the gas flow to increase engine efficiency.
Next to our extensive machining department, we have a complete tube forming department with a large range of tooling for our press brakes, hydraulic presses and other forming equipment.
Tube is formed by the radius punch on the ram, incrementally advancing the flat sheets until a perfect cylinder is created.
Our large tooling range in the forming department means we can form anything from cones and simple folds to complex geometries.


Seam Welding
When the tubes are formed, the cylinder is completed with a seam weld. This high-quality seam weld is automatically created by progressively forming the weld rather than welding the entire joint at once.
The two electrodes in our fully automatic seam welding equipment apply the correct pressure and electrical current needed for that specific exotic material (typically Inconel, titanium or stainless steel) to create the perfect uniform welds. This is done by pressing the semi-molten surfaces together to create a fusion bond.
One of the largest advantages of the seam welding process used at GoodFabs is that the seam welding joint is already forged due to the applied heat, which produces a durable weld which lasts.
To enquire about the cost of formed tube, please contact us specifying your location, as well as quantity, material, diameter and wall thickness required.
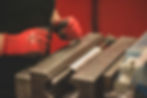

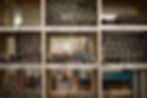

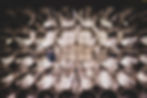
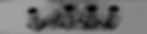
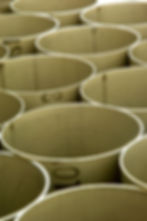
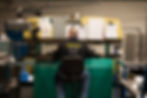
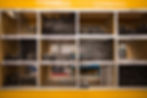
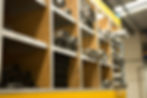